Rechargable Batteries
We have seen in the previous chapter that there are many different types and sizes of EVs. However, in nearly all road vehicles the battery is a key component. In the classical EV the battery is the only energy store, and the component with the highest cost, weight and volume. In hybrid vehicles the battery, which must continually accept and give out electrical energy, is also a key component of the highest importance. Some fuel cell (FC) vehicles have been made which have batteries that are no larger than those normally fitted to IC engine cars, but it is probably that most early FC-powered vehicles will have quite large batteries and work in hybrid FC/battery mode. In short, a good understanding of battery technology and performance is vital to anyone involved with electric road vehicles.
What is an electric battery?
A battery consists of two or more electric cells connected together. The cells convert chemical energy to electrical energy. The cells consist of positive and negative electrodes in an electrolyte. It is the chemical reaction between the electrodes and the electrolyte which generates DC electricity. In the case of secondary or rechargeable batteries the chemical reaction can be reversed by reversing the current and the battery returned to a charged state.
The ‘lead acid’ battery is the traditional rechargeable type, but there are others which are becoming popular in modern EVs. The first EV using rechargeable batteries preceded the invention of the rechargeable lead acid battery by a quarter of a century, and there are a very large number of materials and electrolytes that can be combined to form a battery. However, only a relatively small number of combinations have been developed as commercial rechargeable electric batteries suitable for use in vehicles. At present these include lead acid, nickel iron, nickel cadmium, nickel metal hydride (NiMH), lithium polymer and lithium iron, sodium sulfur and sodium metal chloride. There are also more recent developments of batteries that can be mechanically refuelled, the main ones being aluminium–air and zinc–air. Despite all the different possibilities tried, and about 150 years of development, a suitable battery has only recently been developed which allows mass production of EVs.
From the EV designer’s point of view the battery can be treated as a ‘black box’ that has a range of performance criteria. These criteria will include specific energy, energy density, specific power, typical voltages, amphour efficiency, energy efficiency, commercial availability, cost, operating temperatures, self-discharge rates, number of life cycles and recharge rates – terms which will be explained in the following section. The designer also needs to understand how energy availability varies with ambient temperature, charge and discharge rates, battery geometry, optimum temperature, charging methods, cooling needs and likely future developments. However, at least a basic understanding of the battery chemistry is very important, otherwise the performance and maintenance requirements of the different types, and most of the disappointments connected with battery use, such as their limited life, self-discharge, reduced efficiency at higher currents, and so on, cannot be understood. This basic knowledge is also needed in regard to likely hazards in an accident and the overall impact of the use of battery chemicals on the environment. Recycling of used batteries is also becoming increasingly important.
The main parameters that specify the behaviour and performance of a battery are given in the following section. In the later sections the chemistry and performance of the most important battery types are outlined, and finally the very important topic of battery performance modelling is outlined.
Battery Parameters
Cell and Battery Voltages
All electric cells have nominal voltages which give the approximate voltage when the cell is delivering electrical power. The cells can be connected in series to give the overall voltage required. Traction batteries for EVs are usually specified as 6 V or 12 V, and these units are in turn connected in series to produce the voltage required. This voltage will, in practice, change. When a current is given out, the voltage will fall; on charging, the voltage will rise.
This is best expressed in terms of ‘internal resistance’ and the equivalent circuit of a battery. The battery is represented as having a fixed voltage E, but the voltage at the terminals is a different voltage V , because of the voltage across the internal resistance R. Assuming that a current I is flowing out of the battery, then by basic circuit theory we can say that
\[V = E − IR\]
Note that if the current I is zero, the terminal voltage is equal to E, and so E is often referred to as the open-circuit voltage. If the battery is being charged, then clearly the voltage will increase by IR. In EV batteries the internal resistance should clearly be as low as possible
Generally potential equation gives a fairly good prediction of the ‘in-use’ battery voltage. However, the open-circuit voltage E is not in fact constant. The voltage is also affected by the ‘state of charge’ and other factors such as temperature.
Charge (or Amp hour) Capacity
The electric charge that a battery can supply is clearly a most crucial parameter. The SI unit for this is the coulomb – the charge when 1 A flows for 1 second. However, this unit is inconveniently small. Instead the amp hour is used – 1 A flowing for 1 hour. The capacity of a battery might be, say, ‘10 Ah’. This means that it can provide 1 A for 10 hours, or 2 A for 5 hours, or, in theory, 10 A for 1 hour. However, in practice, it does not work out like this for most batteries.
It is usually the case that while a battery may be able to provide 1 A for 10 hours, if 10 A is drawn from it, it will last less than 10 hours. It is most important to understand this. The capacity of the large batteries used in EVs (‘traction batteries’) is usually quoted for a 5 hour discharge. It is also noted that capacity is affected if the charged is removed more quickly, or more slowly. A nominally 100 Ah battery, if the charge is removed in 1 hour, the capacity falls very considerably to about 70 Ah. On the other hand, if the current is drawn off more slowly, in say 20 hours, the capacity rises to about 110 Ah.
This change is capacity occurs because of unwanted side reactions inside the cell. The effect is most noticeable in the lead acid battery, but occurs in all types. It is very important to be able to predict accurately the effects of this phenomenon.
The charge capacity leads to an important notational point that should be explained here. The capacity of a battery in amphours is represented by the letter C. However, somewhat confusingly, till you get used to it, this is also used to represent a current. Suppose a battery has a capacity of 42 Ah; then it is said that C = 42 A. Battery users talk about ‘a discharge current of 2C’, or ‘charging the battery at 0.4C’. In these cases this would mean a ‘discharge current of 84 A’, or a ‘charging current of 16.8 A’. A further refinement is to use a subscript with the C symbol. As we noted above, the amphour capacity of a battery varies with the time taken for the discharge. In our example, the 42 Ah battery is rated thus for a 10 hour discharge. In this more complete notation, a discharge current of 84 A should be written as 2C10.
Example: Express the current 21 A from our example 42 Ah battery in ‘C’ notation. As a ratio of 42 A, 21 is 1/2 or 0.5. Thus the current 21 A = 0.5C10. This way of expressing a battery current is very useful, as it relates the current to the size of the battery. It is almost universally used in the battery literature and specifications, though the subscript relating to the rated discharge time is often omitted.
Energy Stored
The purpose of the battery is to store energy. The energy stored in a battery depends on its voltage and the charge stored. The SI unit is the joule, but this is an inconveniently small unit, and so we use the watthour instead. This is the energy equivalent of working at a power of 1 W for 1 hour. The watthour is equivalent to 3600 J. The watthour is compatible with our use of the amphour for charge, as it yields the simple formula
Energy in watthours = voltage × amphours, or Energy = V × C
However, this equation must be used with great caution. We have noted that both the battery voltage V and even more so the ampere hour capacity C vary considerably depending on how the battery is used. Both are reduced if the current is increased and the battery is drained quickly. The stored energy is thus a rather variable quantity and reduces if the energy is released quickly. It is usually quoted in line with the amphour rating; that is, if the charge capacity is given for a 5 hour discharge, then the energy should logically be given for this discharge rate.
Specific Energy
Specific energy is the amount of electrical energy stored for every kilogram of battery mass. It has units of Wh kg−1. Once the energy capacity of the battery needed in a vehicle is known (watthours) it can be divided by the specific energy (Wh kg−1) to give a first approximation of the battery mass. Specific energies quoted can be no more than a guide, because, as we have seen, the energy stored in a battery varies considerably with factors such as temperature and discharge rate.
Energy Density
Energy density is the amount of electrical energy stored per cubic metre of battery volume. It normally has units of Wh m−3. It is also an important parameter as the energy capacity of the battery (Wh) can be divided by its energy density (Wh m−3) to show the volume of battery required. Alternatively, if a known volume is available for batteries, the volume (m3) can be multiplied by the battery’s energy density (Wh m−3) to give a first approximation of how much electrical energy can be made available. The battery volume may well have a considerable impact on vehicle design. As with specific energy, the energy density is a nominal.
Specific Power
Specific power is the amount of power obtained per kilogram of battery. It is a highly variable and rather anomalous quantity, since the power given out by the battery depends far more upon the load connected to it than the battery itself. Although batteries do have a maximum power, it is not sensible to operate them at anywhere near this maximum power for more than a few seconds, as they will not last long and would operate very inefficiently.
The normal units are W kg−1. Some batteries have a very good specific energy, but have low specific power – which means they store a lot of energy, but can only give it out slowly. In EV terms, they can drive the vehicle very slowly over a long distance. High specific power normally results in lower specific energy for any particular type of battery. This is because taking the energy out of a battery quickly, that is at high power, reduces the energy available.
This difference in change of specific power with specific energy for different battery types is very important, and it is helpful to be able to compare them. This is often done using a graph of specific power against specific energy, which is known as a ‘Ragone plot’. Logarithmic scales are used, as the power drawn from a battery can vary greatly in different applications. A Ragone plot for a good-quality lead acid traction battery, and a similar NiCad battery.
It can be seen that, for both batteries, as the specific power increases, the specific energy is reduced. In the power range 1–100 W kg−1 the NiCad battery shows slightly less change. However, above about 100 W kg−1 the NiCad battery falls much faster than the lead acid.
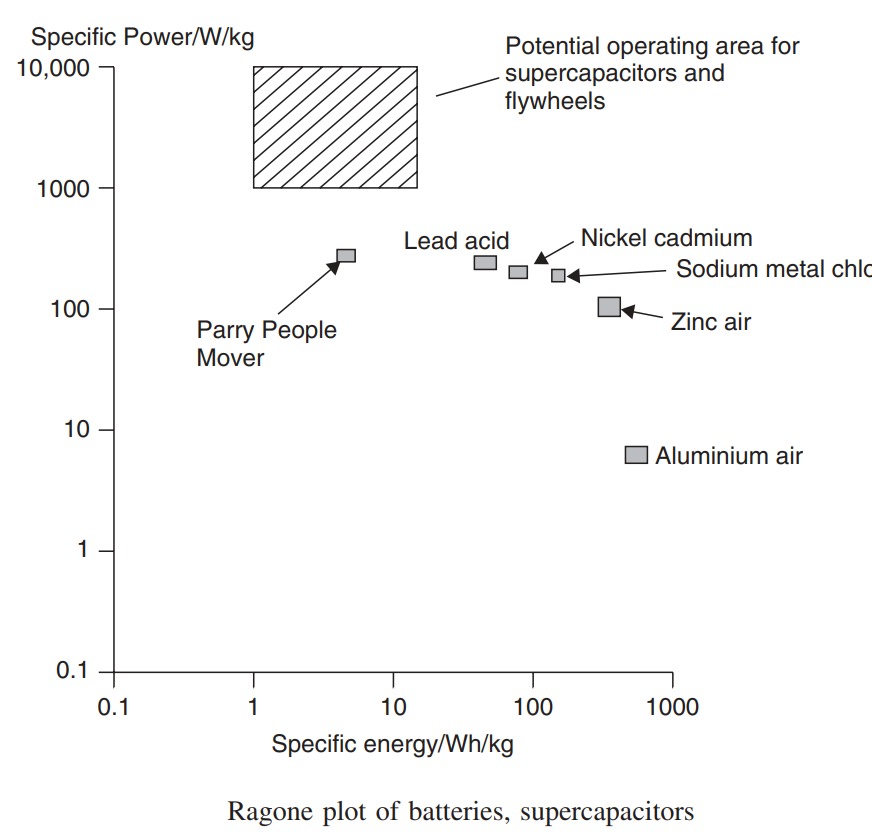
Ragone plots like in the Figure are used to compare energy sources of all types. In this case we should conclude that, ignoring other factors such as cost, the NiCad battery performs better if power densities of less than 100 W kg−1 are required. However, at higher values, up to 250 W kg−1 or more, then the lead acid begins to become more attractive. The Ragone plot also emphasises the point that a simple single-number answer cannot be given to the question ‘What is the specific power of this battery?’
Amp hour (or Charge) Efficiency
In an ideal world a battery would return the entire charge put into it, in which case the amphour efficiency is 100%. However, none do! Their charging efficiency is less than 100%. The precise value will vary with different types of battery, temperature and rate of charge. It will also vary with the state of charge. For example, when charged from about 20–80% charged the efficiency will usually be very close to 100%, but as the last 20% of the charge is put in the efficiency falls off greatly.
Energy Efficiency
This is another very important parameter and it is defined as the ratio of electrical energy supplied by a battery to the amount of electrical energy required to return it to the state before discharge. A strong argument for using EVs is based on the efficient use of energy, with a resulting reduction of overall emissions – hence high energy efficiency is desirable. It should be clear from what has been said in the preceding sections that the energy efficiency will vary very greatly with how a battery is used. If the battery is charged and discharged rapidly, for example, energy efficiency decreases considerably. However, it does act as a guide for comparing batteries, in much the same way as fuel consumption does for cars.
Self-discharge Rates
Most batteries discharge when left unused, and this is known as self-discharge. This is important as it means some batteries cannot be left for long periods without recharging. The reasons for this self-discharge will be explained in the sections that follow. The rate varies with battery type and with other factors such as temperature – higher temperatures greatly increase self-discharge.
Battery Geometry
Cells come in many shapes: round, rectangular, prismatic or hexagonal. They are normally packaged into rectangular blocks. Some batteries can be supplied with a fixed geometry only. Some can be supplied in a wide variation of heights, widths and lengths. This can give the designer considerable scope, especially when starting with a blank sheet of paper – or more likely today a blank CAD screen. The designer could, for example, spread the batteries over the whole floor area ensuring a low centre of gravity and very good handling characteristics.
Battery Temperature, Heating and Cooling Needs
While most batteries run at ambient temperature, some run at higher temperatures and need heating to start with and then cooling when in use. In others, battery performance drops off at low temperatures, which is undesirable, though this problem could be overcome by heating the battery. When choosing a battery the designer needs to be aware of battery temperature, heating and cooling needs and has to take these into consideration during the vehicle design process.
Battery Life and Number of Deep Cycles
Most rechargeable batteries will only undergo a few hundred deep cycles to 20% of the battery charge. However, the exact number depends on the battery type, and also on the details of the battery design and on how the battery is used. This is a very important figure in a battery specification, as it reflects the lifetime of the battery, which in turn reflects the EV running costs.
Lead Acid Batteries
Lead Acid Battery Basics
Until recently the best known and most widely used battery for EVs is the lead acid battery. Lead acid batteries are widely used for starting IC engine vehicles and as such are well known. However, for EVs, more robust lead acid batteries that withstand deep cycling and use a gel rather than a liquid electrolyte are used. These batteries are more expensive to produce.
In the lead acid cells the negative plates have a spongy lead as their active material, while the positive plates have an active material of lead dioxide. The plates are immersed in an electrolyte of dilute sulfuric acid. The sulfuric acid combines with the lead and the lead oxide to produce lead sulfate and water, electrical energy being released during the process. The overall reaction is
\[Pb + PbO_2 + 2 H_2SO_4 ↔ 2 PbSO_4 + 2 H_2O\]
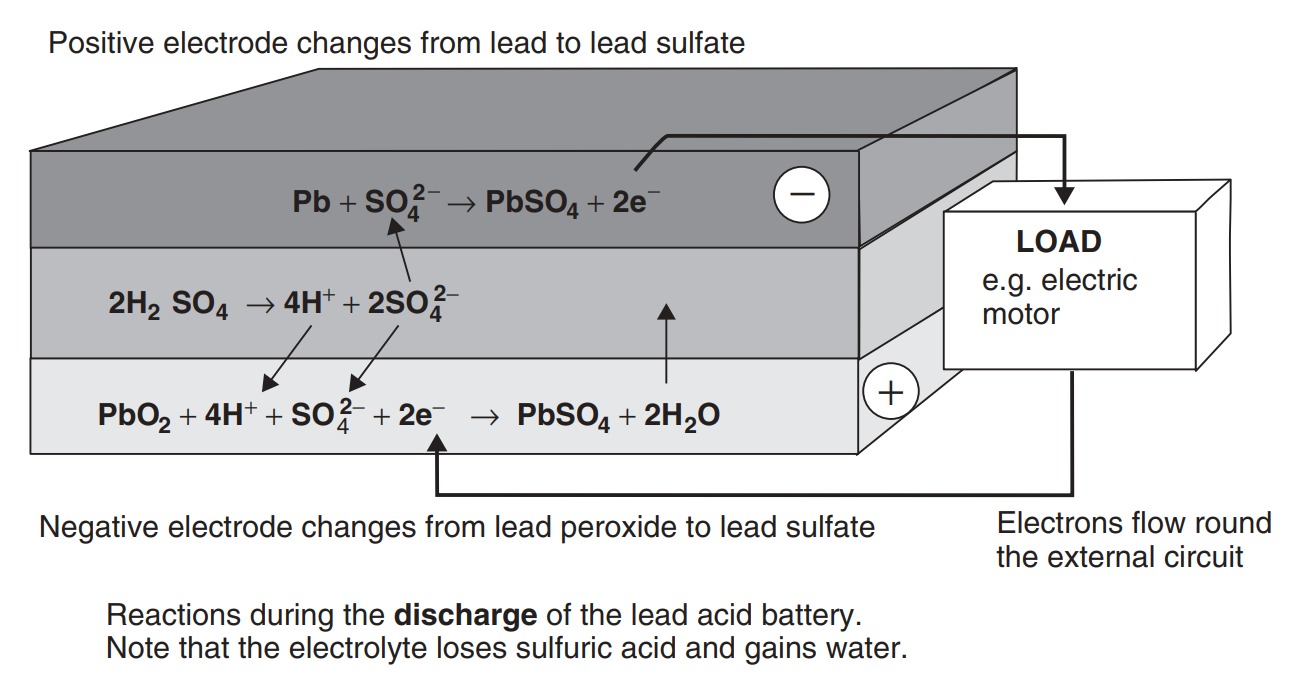
The reactions on each electrode of the battery are shown in Figure. In the upper diagram the battery is discharging. Both electrode reactions result in the formation of lead sulfate. The electrolyte gradually loses the sulfuric acid, and becomes more dilute. When being charged, as in the lower diagram of Figure, the electrodes revert to lead and lead dioxide. The electrolyte also recovers its sulfuric acid, and the concentration rises. The lead acid battery is the most commonly used rechargeable battery in anything but the smallest of systems. The main reasons for this are that the main constituents (lead, sulfuric acid, a plastic container) are not expensive, that it performs reliably, and that it has a comparatively high voltage of about 2 V per cell. The overall characteristics of the battery are given in Table.
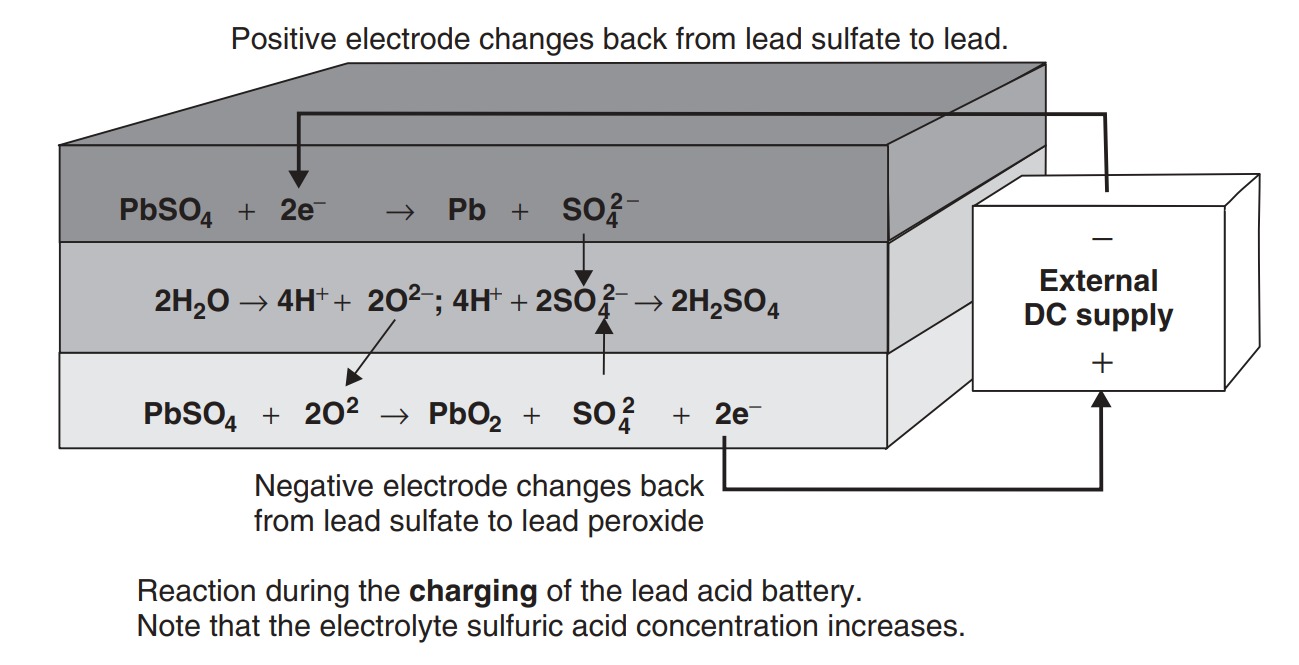
One of the most notable features of the lead acid battery is its extremely low internal resistance. This means that the fall in voltage as current is drawn is remarkably small – probably smaller than for any of the candidate vehicle batteries. The figure given is for a single cell, of nominal capacity 1.0 Ah. The capacity of a cell is approximately proportional to the area of the plates, and the internal resistance is approximately inversely proportional to the plate area. The result is that the internal resistance is, to a good approximation, inversely proportional to the capacity. The figure given of 0.022 per cell is a rule of thumb taken from a range of good-quality traction batteries. A good estimate of the internal resistance of a lead acid battery is thus
\[R = no. of cells × 0.022 C10\]
The number of cells is the nominal battery voltage divided by 2.0, that is six in the case of a 12 V battery. C10 is the amphour capacity at the 10 h rate.
Nominal battery parameters for lead acid batteries | |
---|---|
Specific energy | 20–35 Wh kg−1 depending on usage |
Energy density | 54–95 Wh l−1 |
Specific power | \(\sim\)250 W kg−1 before efficiency falls very greatly |
Nominal cell voltage | 2 V |
Amphour efficiency | \(\sim\)80%, varies with rate of discharge and temperature |
Internal resistance | Extremely low, \(\sim\) 0.022 per cell for 1 Ah cell |
Commercially available | Readily available from several manufacturers |
Operating temperature | Ambient, poor performance in extreme cold |
Self discharge | \(\sim\) 2% per day |
Number of life cycles | Up to 800 to 80% capacity |
Recharge time | 8 h (but 90% recharge in 1 h possible |
Special Characteristics of Lead Acid Batteries
Unfortunately the lead acid battery reactions shown in Equation are not the only ones that occur. The lead and lead dioxide are not stable in sulfuric acid and decompose, albeit very slowly, with the reactions:
At the positive electrode:
\[2 PbO_2 + 2 H_2SO_4 → 2 PbSO_4 + 2 H_2O + O_2\]
At the negative electrode:
\[Pb + H_2SO_4 → PbSO_4 + H_2 \]
This results in the self-discharge of the battery. The rate at which these reactions occur depends on the temperature of the cell – faster if hotter. It also depends on other factors, such as the purity of the components (hence quality) and the precise alloys used to make up the electrode supports.
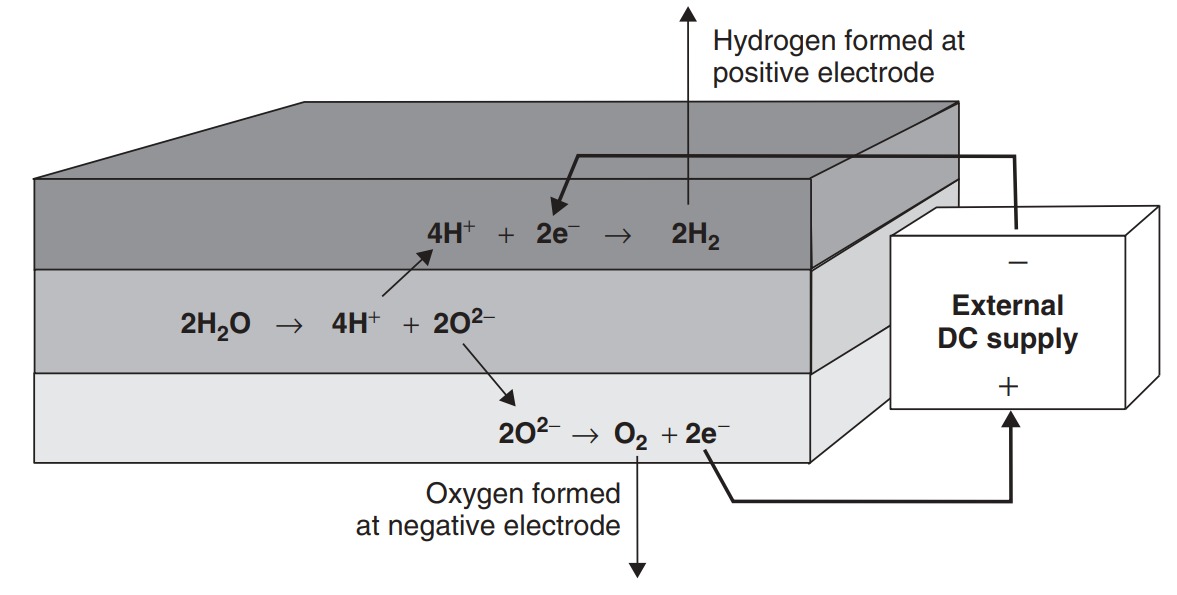
These unwanted reactions, which also produce hydrogen and oxygen gas, also occur while the battery is discharging. In fact they occur faster if the battery is discharged faster, due to lower voltage, higher temperature and higher electrode activity. This results in the ‘lost charge’ effect that occurs when a battery is discharged more quickly. It is a further unfortunate fact that these discharge reactions will not occur at exactly the same rate in all the cells, and thus some cells will become more discharged than others. This has very important consequences for the way batteries are charged, as explained below. But, in brief, it means that some cells will have to tolerate being ‘overcharged’ to make sure all the cells become charged.
The reactions that occur in the lead acid battery when it is being ‘overcharged’. These ‘gassing’ reactions occur when there is no more lead sulfate on the electrodes to give up or accept the electrons. They thus occur when the battery is fully or nearly fully charged.
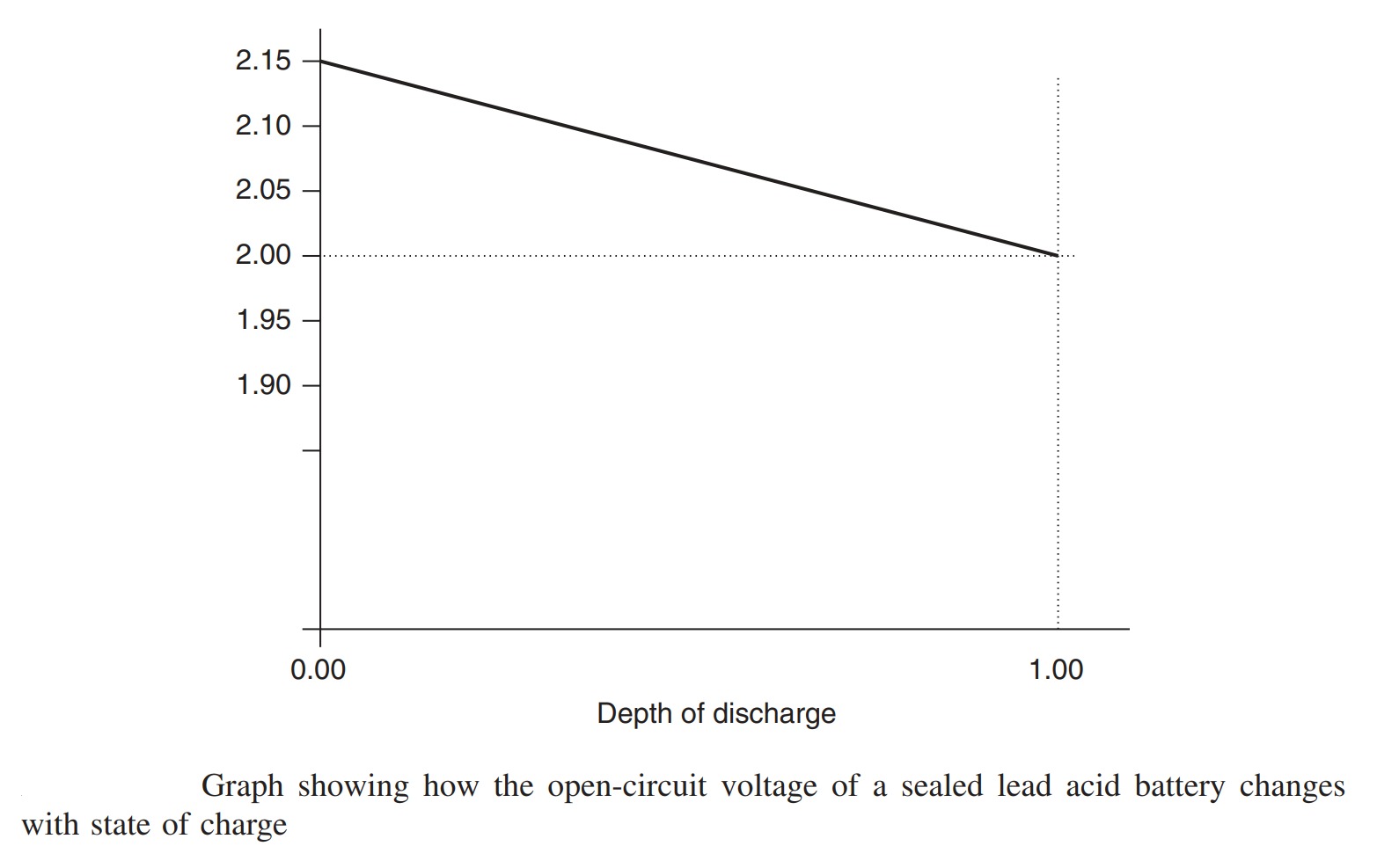
We have noted that the charging and discharging reactions involve changing the concentration of the electrolyte of the cells. The change in concentration of the reactants means that there is a small change in the voltage produced by the cell as it discharges. This decline in voltage is illustrated in Figure. For modern sealed batteries the change is linear to quite a good approximation. It should be noted that this battery voltage cannot normally be used to give an indication of the state of charge of the battery. It is not normally possible to measure this open-circuit voltage when the battery is in use, and in any case it is also greatly affected by temperature, so a chance measurement of the battery voltage is likely to be strongly affected by other factors.
A notable feature of the overcharge reactions and the self-discharge reactions is that water is lost and turned into hydrogen and oxygen. In older battery designs this gas was vented out and lost, and the electrolyte had to be topped up from time to time with water. In modern sealed batteries this is not necessary or even possible. The gases are trapped in the battery and allowed to recombine (which happens at a reasonable rate spontaneously) to reform as water. Clearly there is a limit to the rate at which this can happen, and steps must be taken to make sure gas is not produced too rapidly. This is dealt with in the sections that follow.
Manufacturers of lead acid batteries can supply them in a wide range of heights, widths and lengths, so that for a given required volume they can be fairly accommodating. However, a problem with the wide use of lead acid batteries is that different designs are made for different applications, and it is essential to use the correct type. The type of battery used for the conventional car, the so-called starting, lighting and ignition (SLI) battery, is totally unsuitable for EV applications. Other lead acid batteries are designed for occasional use in emergency lighting and alarms – these are also totally unsuitable. It is only batteries of the ‘traction’ or ‘deep cycling’ type that are suitable here. These are the most expensive type of lead acid battery.
Lithium Batteries
Introduction
Since the late 1980s rechargeable lithium cells have started to come on the market. They offer greatly increased energy density in comparison with other rechargeable batteries, though at increased cost although this is coming down. It is a well-established feature of the most expensive laptop computers and mobile phones that lithium rechargeable batteries are specified, rather than the lower cost NiCad or NiMH cells that we considered earlier.
Up until the advent of lithium batteries, the development of suitable batteries for EVs could arguably be viewed as somewhat pedestrian. Battery development has recently leapt forward considerably and lithium batteries have developed to the point where motor manufacturers are prepared to mass-produce EVs. We have not yet reached the stage where commercial lithium batteries are fully developed, but there are predictions that by 2020 lithium batteries will have specific energies greater than 300 Wh kg−1, approximately 10 times that of lead acid batteries.
The Lithium Polymer Battery
The lithium polymer battery uses lithium metal for the negative electrode and a transition metal intercalation oxide for the positive one. In the resulting chemical reaction the lithium combines with the metal oxide to form a lithium metal oxide and release energy. When the battery is recharged the chemical reaction is reversed. The lithium is thus both a reactant and the mobile ion that moves through the electrolyte. The overall chemical reaction is
\[xLi + M_yO_z ↔ Li_xM_yO_z\]
The solid lithium negative electrode has been a cause of problems with this type of cell, namely safety difficulties and sometimes a decrease in performance due to passivation. Thus these cells have been largely superseded by the lithium ion battery.
The Lithium Ion Battery
Lithium ion batteries are a family of rechargeable types in which lithium ions move from the negative electrode to the positive electrode during discharge, and back when charging. Chemistry, performance, cost and safety characteristics vary across these types. A lithium ion battery is a rechargeable battery in which lithium ions move between the anode and cathode, creating a flow of electricity. Lithium in the anode (carbon material) is ionised and emitted to the electrolyte. Lithium ions move through a porous plastic separator and into the cathode. At the same time, electrons are released from the anode. This becomes an electric current travelling to an outside electric circuit. During charging, lithium ions go from the cathode to the anode through the separator. Since this is a reversible chemical reaction, the battery can be recharged.
The three primary functional components of a lithium ion battery are the anode, cathode and electrolyte. The anode of a conventional lithium ion cell is made from carbon, the cathode is a metal oxide, and the electrolyte is a lithium salt in an organic solvent. The most commercially popular anode material is graphite. The cathode is generally one of three materials: a layered oxide (such as lithium cobalt oxide), a polyanion (such as lithium iron phosphate) or a spinel (such as lithium manganese oxide). The electrolyte is typically a mixture of organic carbonates. Depending on the choice of materials, the voltage, capacity, life and safety of a lithium ion battery can change dramatically. Recently, novel architectures using nanotechnology have been employed to improve performance.
Pure lithium reacts vigorously with water so that a non-aqueous electrolyte is used, and a sealed container rigidly excludes water from the battery pack. Lithium ion batteries are more expensive than NiCad batteries but operate over a wider temperature range with higher energy densities, while being smaller and lighter. They are fragile and so need a protective circuit to limit peak voltages. Initially used for consumer electronics, the lithium ion battery (LIB) is growing in popularity for EV applications. Research is yielding a stream of improvements to traditional LIB technology, focusing on energy density, durability, cost and safety.
The LIB was introduced in the early 1990s and used a lithiated transition metal intercalation oxide for the positive electrode and lithiated carbon for the negative electrode. The electrolyte is either a liquid organic solution or a solid polymer. Electrical energy is obtained from the combination of the lithium carbon and the lithium metal oxide to form carbon and lithium metal oxide. The overall chemical reaction for the battery is
\[Li_x + M_yO_z ↔ 6 C + Li_xM_yO_z\]
The essential features of the battery are given in Table. An important point about LIBs is that accurate control of voltage is needed when charging lithium cells. If it is slightly too high it can damage the battery; too low and the battery will be insufficiently charged. Suitable commercial chargers are being developed along with the battery. The LIB has a considerable weight advantage over other battery systems and this makes it a highly attractive candidate for EVs. The specific energy, for example, is about three times that of lead acid batteries, and this could give a car a very reasonable range. However, large batteries have until recently been prohibitively expensive, though the price has now dropped to the point where the LIB is the preferred battery for EVs. With recent developments and improved specific energies large companies have set up production lines.
As with most components a ready market combined with quantity production often leads to rapid development and further price reductions. Most modern EVs including the Nissan Leaf, the Mitsubishi MiEV, the Tesla Roadster and the Chevrolet Volt use LIBs. The battery in the Leaf has a capacity of 24 kWh and the specific energy of the cells is 140 Wh kg−1. The predicted development of the battery by 2015 will give a specific energy of 200 Wh kg−1
Nominal properties of lithium ion batteries | |
---|---|
Specific energy | 140 Wh kg−1 |
Energy density | 250–620 Wh l−1 |
Specific power | 300–1500 W kg−1 |
Nominal cell voltage | 3.5 V |
Amphour efficiency | Very good |
Internal resistance | Very low |
Commercially available | Larger LIBs have become the standard battery for electric road vehicles |
Operating temperature | Ambient |
Self-discharge | Very low, \(\sim\) 10% per month |
Number of life cycles | >1000 |
Recharge time | 2–3 h, but can be charged to 80% of their capacity in under 1 h |